Industry Trends and Challenges: Thurston Group: Leading Innovation in Offsite Manufacturing
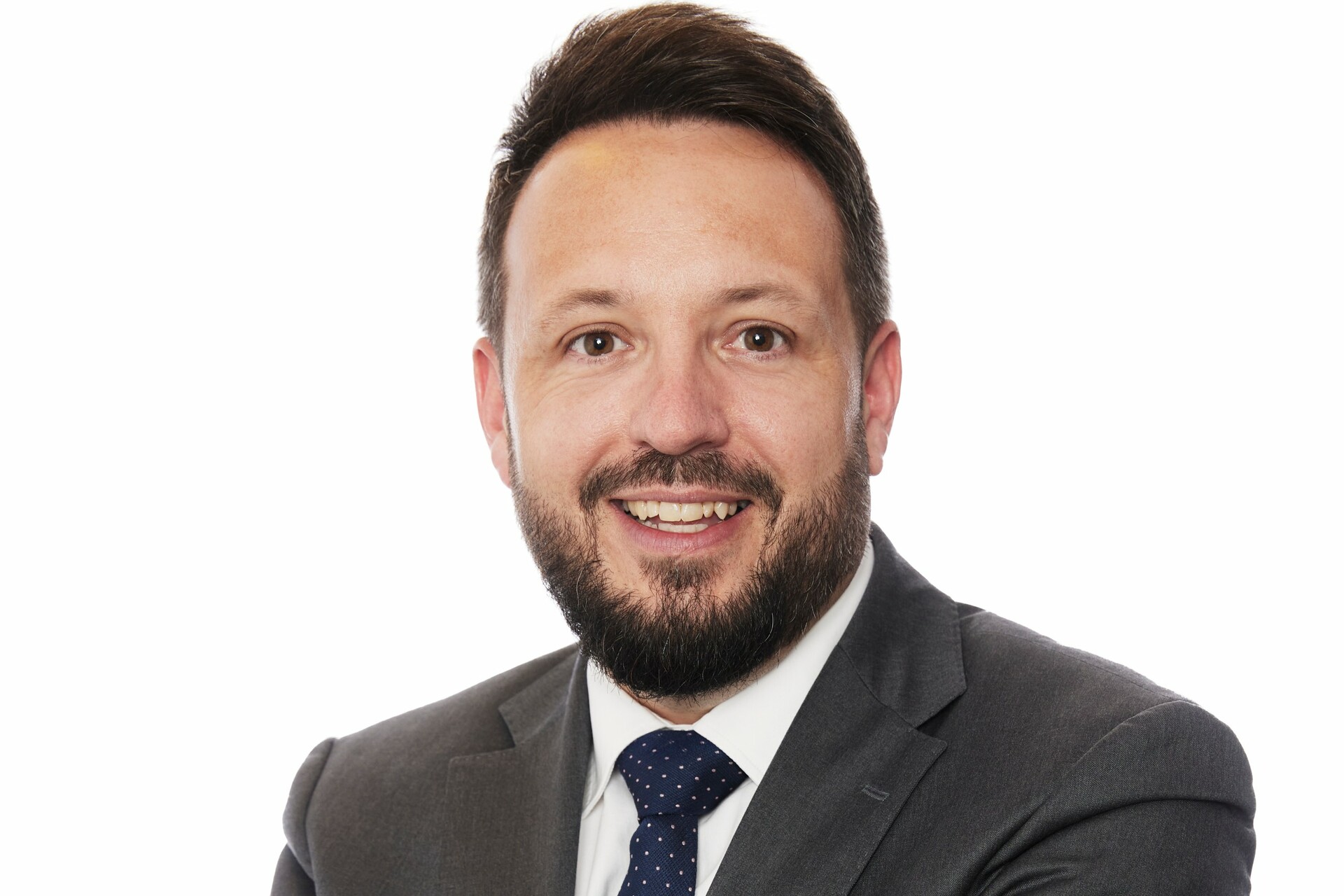
By Marie Carter-Robb
Thurston Group, based in Wakefield, is a leading UK offsite manufacturer of bespoke portable and modular buildings. Supplying a diverse range of sectors-including logistics, nuclear, education, healthcare, meanwhile housing, and welfare accommodation-the company is at the forefront of innovation in construction. Managing Director Matt Goff has led the company through an exceptional period of growth since joining in 2018, championing innovation and development with the aim of positioning Thurston as the offsite manufacturing partner and employer of choice in the UK.
Thurston Group, based in Wakefield, is a leading UK offsite manufacturer of bespoke portable and modular buildings. Supplying a diverse range of sectors-including logistics, nuclear, education, healthcare, meanwhile housing, and welfare accommodation-the company is at the forefront of innovation in construction. Managing Director Matt Goff has led the company through an exceptional period of growth since joining in 2018, championing innovation and development with the aim of positioning Thurston as the offsite manufacturing partner and employer of choice in the UK.
Industry Trends and Challenges
What do you see as the most significant trends currently shaping the manufacturing and engineering industries?
Sustainability is a key driver across industries, and its influence on manufacturing, engineering, and construction is undeniable. Thurston Group has made significant investments in product testing, infrastructure, and green technologies, earning recognition as one of the UK’s top-performing offsite manufacturers in the Plimsoll Modular Construction Market Report.
The company has worked closely with clients to refine specifications and develop energy-efficient product offerings, particularly in education and construction site welfare accommodation. Customers increasingly demand sustainable solutions, alongside greater transparency in environmental practices. Thurston Group embraces a partnership approach, working collaboratively with supply chain partners to advance sustainability innovations within offsite manufacturing.
What are the biggest challenges your company is facing right now, and how are you addressing them?
The modular construction industry has faced considerable challenges, with some competitors ceasing operations due to economic pressures. Thurston Group has taken a different approach-focusing on sustainable growth, diversification, and operational agility.
By avoiding high-risk projects and concentrating on core strengths, the company has maintained a steady market position. Its ability to manufacture at least 50% of its product range across multiple facilities ensures flexibility and resilience. Project delays remain a major risk in construction, and Thurston is advocating for a shift towards clearer, more reliable timelines within the industry.
Additionally, rising national insurance costs pose financial challenges, yet the company remains committed to its workforce, continuing to invest in learning and development. As the business expands, it also ensures that smaller projects remain viable alongside large contracts, reinforcing its dynamic and adaptable approach.
Embracing Innovation and Technology
How is your company leveraging new technologies like automation, AI, or IoT to stay competitive?
Automation plays an increasing role in offsite manufacturing. While full-scale robotics are not yet viable in the sector due to the bespoke nature of projects, Thurston Group focuses on incremental efficiency gains.
One major investment has been in business-wide software that connects every department, providing real-time data insights. This system allows for proactive issue resolution, enhances workflow efficiency, and has enabled a paperless operation. The company is also leveraging Building Information Modelling (BIM) to improve planning accuracy, reduce waste, and enhance collaboration.
While AI has not yet been formally adopted, Thurston continues to explore its potential applications, ensuring any future integration offers clear, tangible benefits.
Can you share an example of a recent innovation at your company and its impact on operations?
Thurston Group became the first manufacturer in its industry to achieve an EPC A rating for modular cabins while maintaining the highest fire safety standards. Achieved through a £250,000 investment, this milestone preceded strict new regulatory changes, reinforcing the company’s leadership in safety and compliance. The company’s in-house design team continues to push boundaries in fire performance capabilities, ensuring Thurston remains at the forefront of safety and sustainability.
Sustainability and the Future of Manufacturing
What steps is your company taking to reduce its environmental footprint and improve sustainability?
Sustainability is embedded in Thurston’s operations. The company undertakes comprehensive environmental impact assessments across its manufacturing facilities, working with external specialists to identify strategic improvements.
Beyond delivering energy-positive projects, Thurston focuses on circular construction principles-designing modular units for refurbishment and reuse. Enhanced insulation, double glazing, and low-energy electrical systems are standard, with measurable performance data ensuring clients can validate their sustainability credentials.
Environmental, Social, and Governance (ESG) commitments extend beyond green initiatives, with Thurston actively engaging with industry peers to share knowledge and drive collective sustainability progress.
How do you see sustainability influencing the future of manufacturing and engineering?
Customers increasingly favour businesses that prioritise sustainability, and this trend is set to continue. The industry must invest further in sustainable building methods, such as offsite construction, which inherently reduces waste and energy consumption.
A greater emphasis on modular buildings will also support the UK in meeting quotas for schools, housing, and healthcare facilities while contributing to long-term environmental goals-particularly in the North.
Workforce Development and Industry Growth
What skills do you believe are most critical for the future workforce in manufacturing and engineering?
A willingness to learn and adapt is the most critical skill for the future workforce. The rapid pace of change requires individuals to develop multiple competencies, whether through on-the-job training, mentoring, or further education.
While AI continues to automate white-collar tasks, blue-collar roles remain in high demand. However, Thurston believes in a balanced workforce, where individuals transition from hands-on roles into leadership positions-ensuring valuable industry knowledge is retained at all levels.
How is your company investing in workforce development and training?
Thurston Group has invested over £140,000 in workforce training, delivering 100 sector-specific sessions in welding, powered access equipment, and essential skills like first aid and fire safety.
The company also runs a year-long leadership development programme for its executive and senior leadership teams, reinforcing a culture of accountability and growth. By strengthening individual skills, Thurston ensures collective success.
Managing Globalisation and Supply Chain Resilience
How has globalisation affected your business, and how do you manage risks associated with global supply chains?
Thurston prioritises local sourcing, with the majority of its materials procured within a 30-mile radius of its manufacturing sites. However, recognising that suppliers remain influenced by global conditions, the company has adopted a strategic approach to risk management.
Increased in-house manufacturing capabilities, bulk sourcing of raw materials, and strong supplier relationships have reduced reliance on external providers. Post-pandemic, this approach has ensured minimal disruption while meeting growing demand.
What strategies are you employing to ensure resilience and flexibility in your supply chain?
Offsite construction’s prefabrication model allows for greater quality control and planning advantages over traditional methods. By maintaining reserves of key materials and working closely with suppliers, Thurston mitigates supply chain risks while ensuring timely project delivery.
Innovation Culture and Future Vision
How do you maintain a culture of innovation and continuous improvement within your organisation?
Thurston fosters a culture of innovation by empowering employees to challenge conventions and contribute new ideas. The company prioritises knowledge sharing, continuous learning, and solution-based thinking.
Collaboration is also key-Thurston partners with businesses across multiple industries, gaining fresh insights and best practices. Its recent membership in the Made In Yorkshire network further strengthens its ability to drive innovation and efficiency.
What is your vision for the future of your company, and how do you plan to achieve it?
Thurston Group aims to cement its position as a leader in offsite manufacturing by continuing to invest in staff, infrastructure, and sustainable technologies. Strong client relationships remain a cornerstone of its success, setting it apart from competitors.
With a commitment to pushing boundaries, embracing innovation, and maintaining steady growth, the company is well-positioned to shape the future of modular construction in the UK.