Industry Trends and Challenges: An Interview with DefProc Engineering
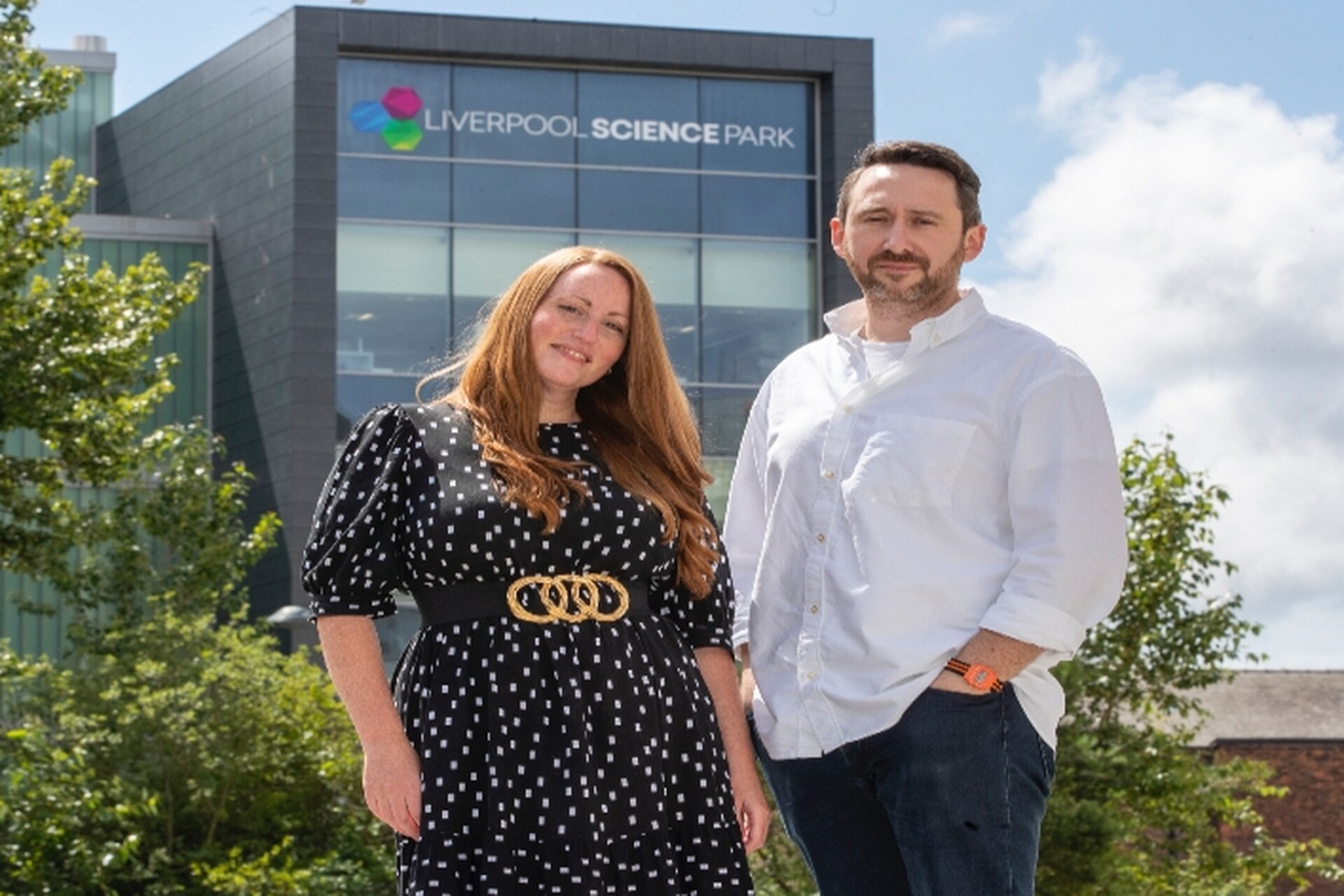
By Marie Carter-Robb
In the first of our exciting new interview series, Industry Trends and Challenges, Northern Engineer sat down with Jen and Patrick Fenner, the dynamic co-founders of Liverpool-based DefProc Engineering.
In the first of our exciting new interview series, Industry Trends and Challenges, Northern Engineer sat down with Jen and Patrick Fenner, the dynamic co-founders of Liverpool-based DefProc Engineering.
Founded in 2013, DefProc Engineering is a design engineering company specialising in product development, small-scale manufacturing, and technical support. The company's services span design, proof of concept, prototyping, and producing scalable products. Jen serves as the Managing Director, contributing her expertise to the Liverpool City Region Combined Authority’s Advanced Manufacturing Board, while Patrick, as the Head of Engineering, is a key initiator of The Things Network Liverpool community.
What do you see as the most significant trends currently shaping the manufacturing and engineering industries?
Upskilling workforces to take advantage of new and existing technologies across the production line. Also, refining automation processes to collect data in one place and then using Generative AI tools to transform this data into useful information, trends and alerts for when stock needs ordering or machines need servicing.
What are the biggest challenges your company is facing right now, and how are you addressing them?
The cost of business from electronics to staff wages has increased dramatically and has been difficult to keep on top of. To combat this, we’ve changed the scope of what we want to do as a business—focusing on long-term projects and diversifying our services.
How is your company leveraging new technologies like automation, AI, or IoT to stay competitive?
We use all of these tools for client projects, for example, on water sensors for trash screens. Before automation, each trash screen was checked manually but now this is automatic; IoT sends the measurement to a system and AI flags when the trash screen will need to be cleared.
Can you share an example of a recent innovation at your company and its impact on your operations?
Smart Gas Pressure Sensor for Northern Gas Networks offers near-real-time data monitoring at the point of supply and employs automation to shut off the gas supply if the pressure drops below the acceptable threshold. Smart Gas accommodates natural gas, blended, or 100% hydrogen supply, ensuring compatibility with evolving infrastructure.
What steps is your company taking to reduce its environmental footprint and improve sustainability?
We are designing for repair rather than disposal. This gives our clients a sustainable income; for example, if a healthcare product is only required for six months, it's cheaper for our client to give it back to us to refurbish or repair and then issue to a new user.
How do you see sustainability influencing the future of manufacturing and engineering?
Waste management is a huge problem that needs to be addressed to make the manufacturing and engineering sector more sustainable. There is no accountability for the waste that is generated currently—products need to have two or three life cycles, and that is the responsibility of the manufacturer.
What skills do you believe are most critical for the future workforce in manufacturing and engineering?
Understanding how AI works and its benefits for collecting data, noticing trends and problem-solving to create efficiency and productivity in the workplace. It’s essential that people of all ages and experience levels recognise its importance and that it's not a threat—it will create autonomy for all.
How is your company investing in workforce development and training?
Everyone has personal development plans tailored to them. These identify opportunities, training, and goals for staff and are reviewed every three months. As a small company, it can be challenging to provide career progression, but this way, everyone can manage their growth and development and work towards their desired objectives.
How has globalisation affected your business, and how do you manage risks associated with global supply chains?
We had to change what we were doing during the pandemic and design products with materials that were available. This included forecasting what parts may be at risk, buying more in one go, and buying them early to ensure our clients’ products could be scaled into the future.
What strategies are you employing to ensure resilience and flexibility in your supply chain?
We differ from other manufacturers because we do initial design and design for manufacture. If we have an unrecoverable parts shortage, we have the in-house capabilities to redesign the product to meet this shortage. We can problem-solve and be flexible at all stages of production from start to finish.
How do you maintain a culture of innovation and continuous improvement within your organisation?
R&D spend has changed over the last few years, so we are constantly reviewing the services we offer to clients. As an innovation partner, we support companies applying for grants, showcase how innovation will impact them, and how we can produce prototypes/products in more efficient and innovative ways.
What is your vision for the future of your company, and how do you plan to achieve it?
We’ve transitioned from doing lots of small projects to fewer, longer-term projects, taking clients from proof of concept to commercialisation with seamless continuity. We’re looking to add a consultancy-focused service to the business to help clients understand where they are in terms of Technology Readiness Level (TRL).
Jen and Patrick Fenner’s leadership at DefProc Engineering exemplifies the innovative spirit needed to navigate the evolving landscape of the manufacturing and engineering sectors. Through a focus on sustainability, workforce development, and leveraging cutting-edge technology, they are steering their company towards a future defined by resilience and adaptability.